Mezzanine Floor Construction in Kansas City, MO
Kansas City Flooring Company now offers expert mezzanine floor construction services that transform your existing space into a more functional environment. Our professional team handles everything from initial design to final installation, creating custom mezzanine solutions that effectively double your usable square footage without the cost of expansion or relocation.
With over three decades in the flooring industry, we've expanded our expertise to include industrial and commercial mezzanine systems. These versatile platforms provide the perfect solution for businesses needing additional storage, office space, or production areas. We carefully assess your specific needs to design a mezzanine floor that integrates seamlessly with your existing operations.
We pride ourselves on delivering high-quality mezzanine floors that meet all safety standards and building codes in Kansas City and surrounding areas. Our comprehensive service includes structural engineering, permit acquisition, and professional installation by our experienced team. Whether you need a small storage platform or a full warehouse mezzanine system, we work efficiently to minimize disruption to your business operations while maximizing your space potential.
Mezzanine Construction Process
Our mezzanine floor construction services go beyond simply adding an extra level to your space. We integrate these structures with your existing operations while optimizing the entire environment for maximum efficiency and functionality.
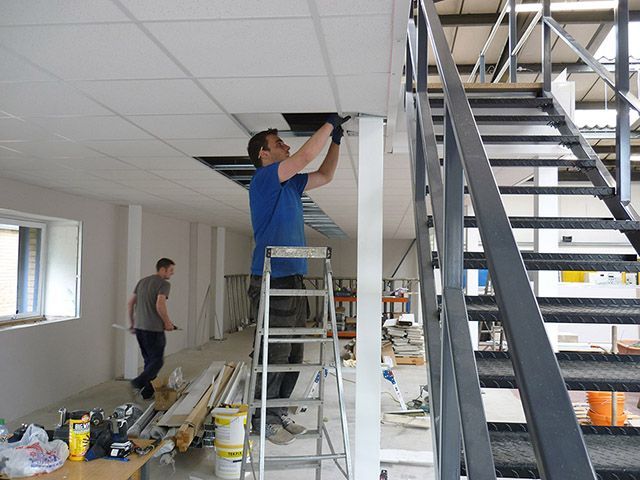
1. Custom Design Approach
We start every mezzanine project with a thorough consultation to understand your specific requirements. Our team works with you to develop customized mezzanine layouts that maximize your available space. Whether you need additional storage, office space, or a retail area, we create engineering blueprints tailored to your building's structure.
2. Timeline and Coordination
We begin by establishing a realistic timeline for your warehouse mezzanine installation. Most standard projects take between 2-4 weeks, depending on size and complexity. Our project managers coordinate with all contractors and your team to create a schedule that works for your business.
3. Safety and Compliance
We strictly adhere to all construction safety standards throughout the installation process, including OSHA requirements and local building codes.
4. Inspection and Testing
Once we complete your mezzanine installation, rigorous inspection and testing become our top priority. We conduct platform load testing to verify that your new structure meets all specified weight requirements. This isn't just a formality—it's essential for safety.
5. Upgrades and Maintenance
Your mezzanine floor will serve you for years, but regular maintenance ensures optimal performance. We recommend quarterly inspections of high-traffic areas to identify potential issues early.
Key Components of Mezzanine Construction
Building a quality mezzanine floor requires careful attention to several critical elements. The structural integrity and safety features work together to create a durable and code-compliant addition to your space.
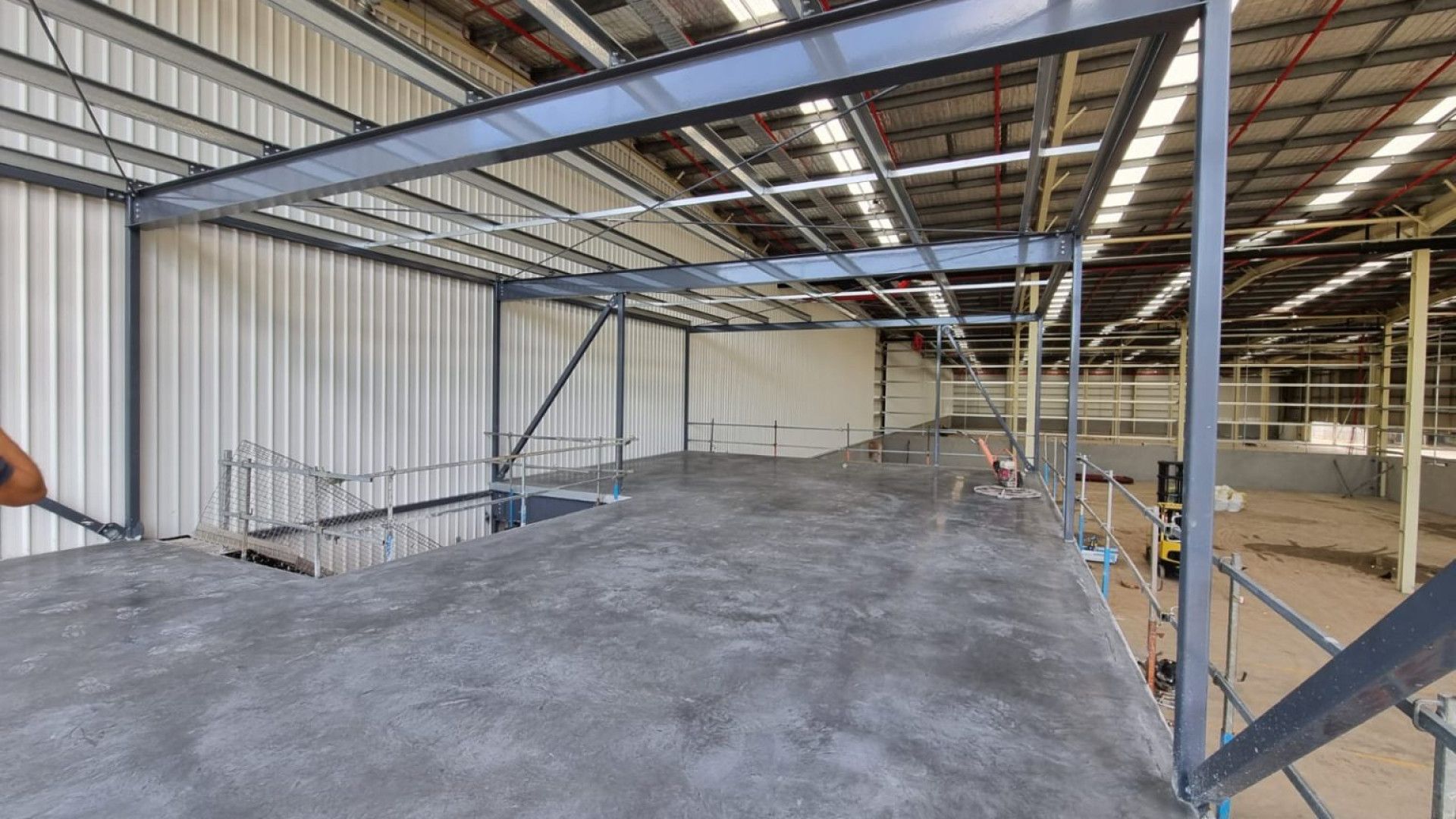
Structural Elements
Our mezzanine floors are built with heavy-duty support systems designed to handle significant weight loads. We use structural steel frameworks as the foundation of every installation, ensuring maximum stability and longevity. These frameworks include strategically placed steel support columns that distribute weight evenly across the entire structure.
The flooring system typically consists of a composite steel deck with a plywood overlay. This combination provides excellent strength-to-weight ratio and creates a smooth, even surface for your operations. Depending on your needs, we can adjust the load-bearing capacity from 125 to 300 pounds per square foot.
Our team carefully engineers each component to work together seamlessly. We consider ceiling height, existing structural elements, and your specific usage requirements when designing the framework.
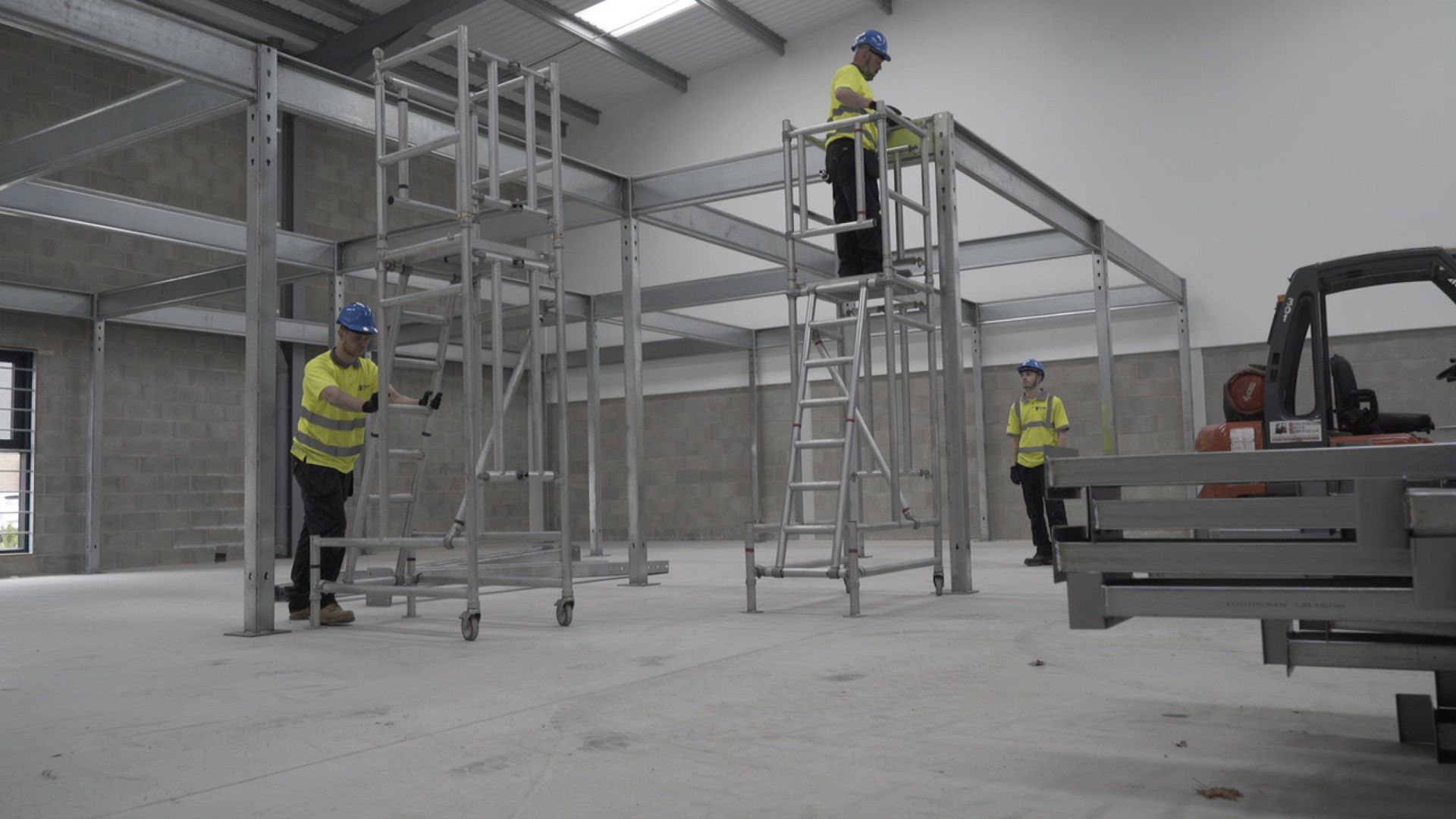
Safety Features
Safety is never optional in mezzanine construction. We install robust safety railings around all open sides of your mezzanine floor, meeting or exceeding all local building codes. These guardrails prevent falls and create a secure working environment for your team.
Fire-code compliance is another critical safety aspect we address. This may include installing proper fire-rated materials, sprinkler systems, and ensuring adequate emergency exits.
Access points receive special attention with properly designed staircases and gates. For material handling, we offer various gate options including swing, sliding, and lift gates that allow safe movement of goods while maintaining fall protection.
All our installations comply with OSHA requirements for handrail height, mid-rails, and toe boards. We also provide proper signage indicating weight limits and safety protocols to ensure safe daily operations.
Benefits of Adding a Mezzanine Floors
Double your available space without the cost of expansion or relocation. You're essentially gaining a new floor at a fraction of construction costs.
Improve workflow efficiency by organizing different operations vertically. You can separate inventory, create office space, or add dedicated areas for specialized tasks.
Quick installation compared to traditional construction means minimal disruption to your operations. Most of our mezzanine projects are completed in days rather than months.
Flexible design options allow your mezzanine to grow with your business. We can design systems that can be expanded or modified as your needs evolve.
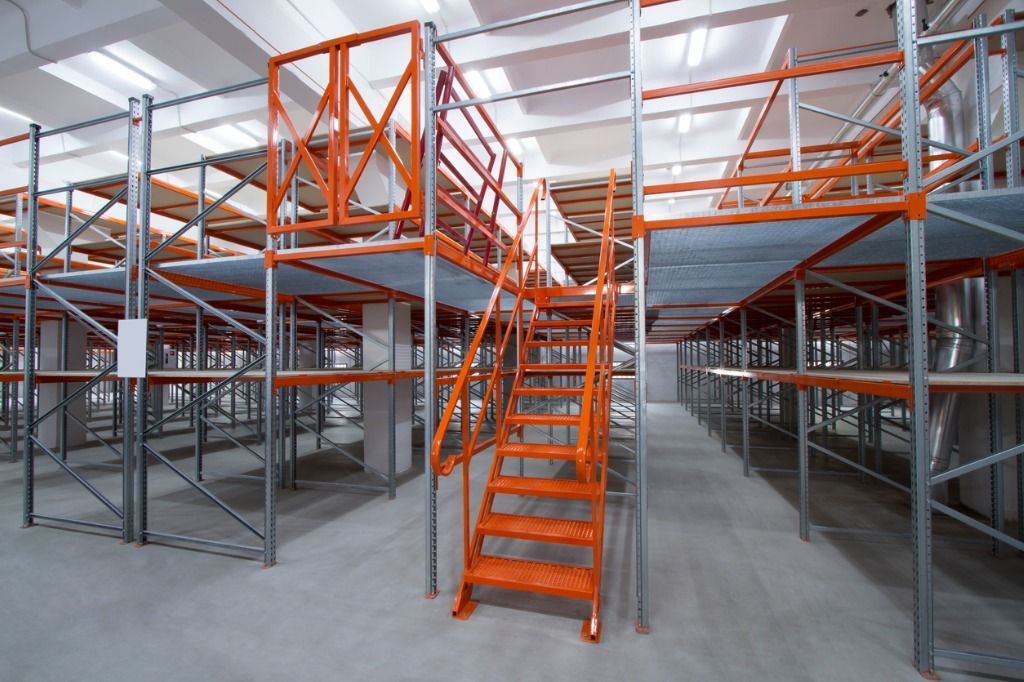
Regulatory and Inspection Criteria
We manage the entire permit acquisition process for your mezzanine floor construction. Our experts are well-versed in Kansas City's building codes and IBC requirements specific to mezzanine structures. The process typically begins with submitting detailed construction plans that include load calculations and structural specifications.
Your mezzanine project must comply with size limitations, which generally restrict the floor area to one-third of the room below. We prepare all documentation needed for zoning approvals and building permits, including:
- Architectural drawings and blueprints
- Structural engineering reports
- Egress and fire safety plans
- Material specifications
Our team coordinates with local building departments to ensure your warehouse mezzanine meets all regulatory criteria before construction begins.
Obtaining Necessary Permits
Once construction is complete, your mezzanine must pass several safety inspections. We coordinate these inspections and ensure your structure meets all requirements. Our installation compliance checks include thorough examination of:
- Guardrail height and strength (minimum 42" height per OSHA standards)
- Staircase dimensions and handrail placement
- Load capacity verification (typically 125 lbs/sq ft for light storage)
- Fire resistance ratings
We perform platform load testing to confirm your mezzanine can safely handle its designated weight capacity. This includes both static and dynamic load testing to verify structural integrity.
Our onsite inspection services don't end after construction. We provide follow-up evaluations to ensure continued compliance as your needs evolve.
Safety Inspections and Tests
Still have a question?
Call us now at (816) 555-0123 or fill out our simple contact form on our website. We'll respond within 24 hours to discuss your specific requirements.