Polyaspartic Floor Coating in Kansas City, MO
Polyaspartic floor coatings have become a top choice for many property owners. These high-performance systems offer superior protection compared to traditional options like epoxy. Polyaspartic coatings deliver unmatched durability and strength, making them perfect for high-traffic areas such as garages, schools, shops, and commercial spaces.
We've seen firsthand how polyaspartic coatings transform concrete floors. This advanced coating innovation is known for its fast drying time, making installation quicker and more convenient for you. Unlike other floor coatings, polyaspartics can be applied both indoors and outdoors, giving you flexibility for various projects. The coating creates a seamless surface that resists chemicals, impacts, and abrasion - problems that damage ordinary floors over time.
Our polyaspartic floor coatings provide long-lasting protection without sacrificing appearance. You can choose from various finishes and colors to match your style preferences. While pricing varies based on factors like garage size and surface preparation needs (including crack repairs), the investment pays off through extended floor life and reduced maintenance. Many of our customers find the combination of durability, quick installation, and aesthetic appeal well worth the cost compared to repeatedly repairing damaged concrete.
Short title
What Is Polyaspartic Floor Coating?
Polyaspartic coating is a specialized type of aliphatic polyurea system that creates a 100% solid, two-component protective layer for concrete floors. This advanced resin technology was developed as a more versatile alternative to traditional coatings. The formulation consists of polyaspartic aliphatic polyurea resins that cure through a chemical reaction when the two components are mixed.
Unlike other coatings, polyaspartics contain low VOCs (Volatile Organic Compounds), making them more environmentally friendly. The chemical structure gives these coatings their distinctive properties including UV stability, which prevents yellowing over time.
We formulate our polyaspartic systems to bond directly with properly prepared concrete. This creates a high-performance floor finish that becomes an integral part of your floor surface.
Epoxy Coatings vs Polyaspartic Coating
Polyaspartic coatings offer several advantages over traditional epoxy systems. While epoxy provides good durability, it remains vulnerable to abrasion, scratching, and chipping.
In contrast, our polyaspartic flooring is more flexible and resistant to these common issues. Installation time represents another major difference. Epoxy requires 3-5 days for complete installation and curing
On the other hand, polyaspartic systems can be applied and ready for use within 24 hours in many cases. Polyaspartics can be installed in temperatures ranging from 0°F to 100°F, while epoxy applications are limited to narrower temperature ranges.
UV stability is another advantage of polyaspartic coatings. Unlike epoxy, which tends to yellow with sun exposure, our polyaspartic systems maintain their color and clarity for years.
Application Areas for Polyaspartic Coatings
Polyaspartic coatings have become increasingly popular due to their versatility and exceptional performance in various environments. These durable floor systems offer protection while enhancing appearance across multiple settings.
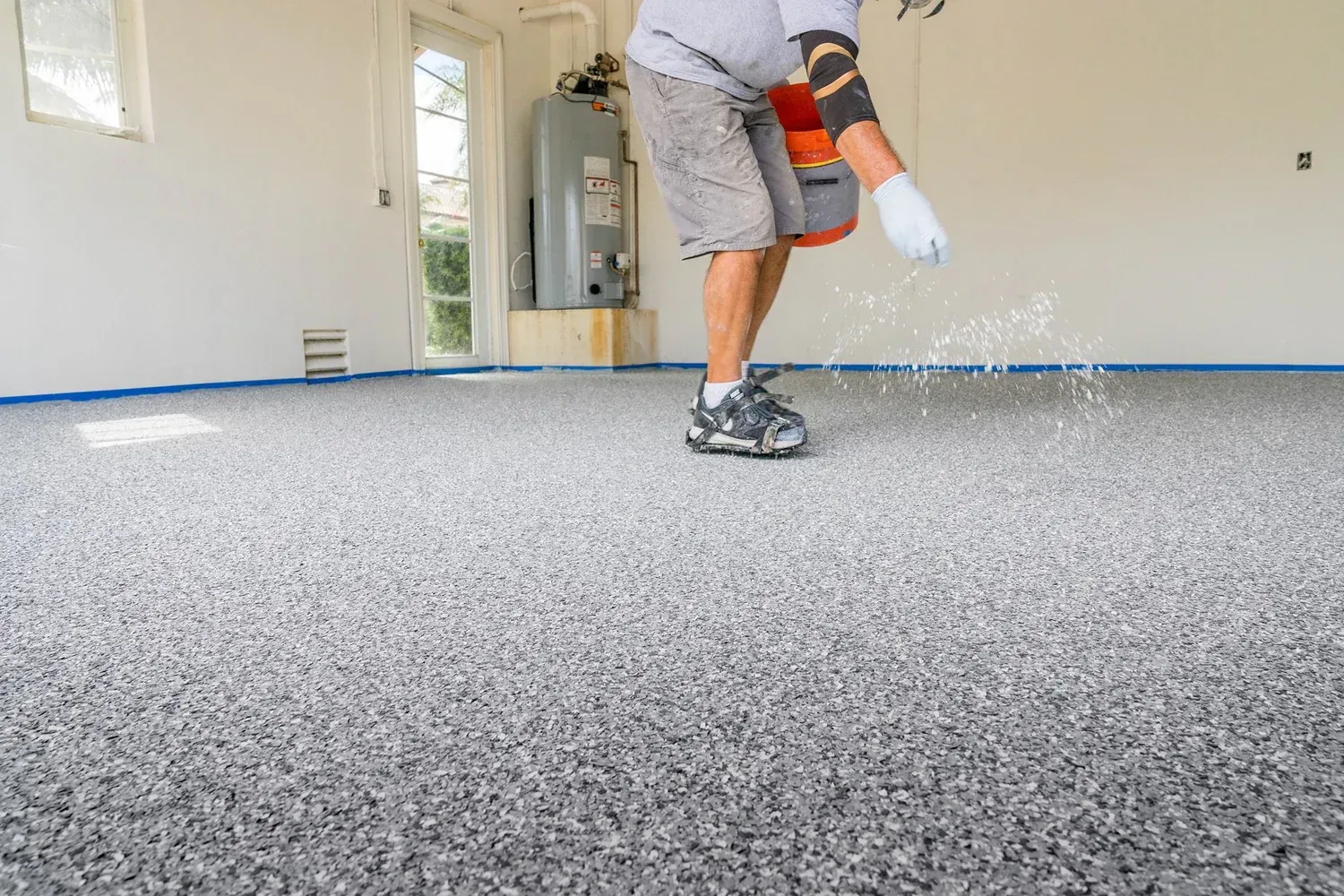
Commercial and Industrial Flooring
In commercial and industrial settings, polyaspartic coatings excel where durability and safety are paramount. Factories, warehouses, and manufacturing facilities benefit from these coatings because they create a seamless floor surface that withstands heavy machinery and frequent foot traffic.
Hospitals and healthcare facilities choose polyaspartic coatings for their antibacterial properties. The non-porous surface prevents bacteria growth and simplifies cleaning protocols.
We've installed these systems in commercial kitchens where food-grade coating requirements are strict. The chemical resistance protects against acids, oils, and cleaning agents common in food preparation areas.
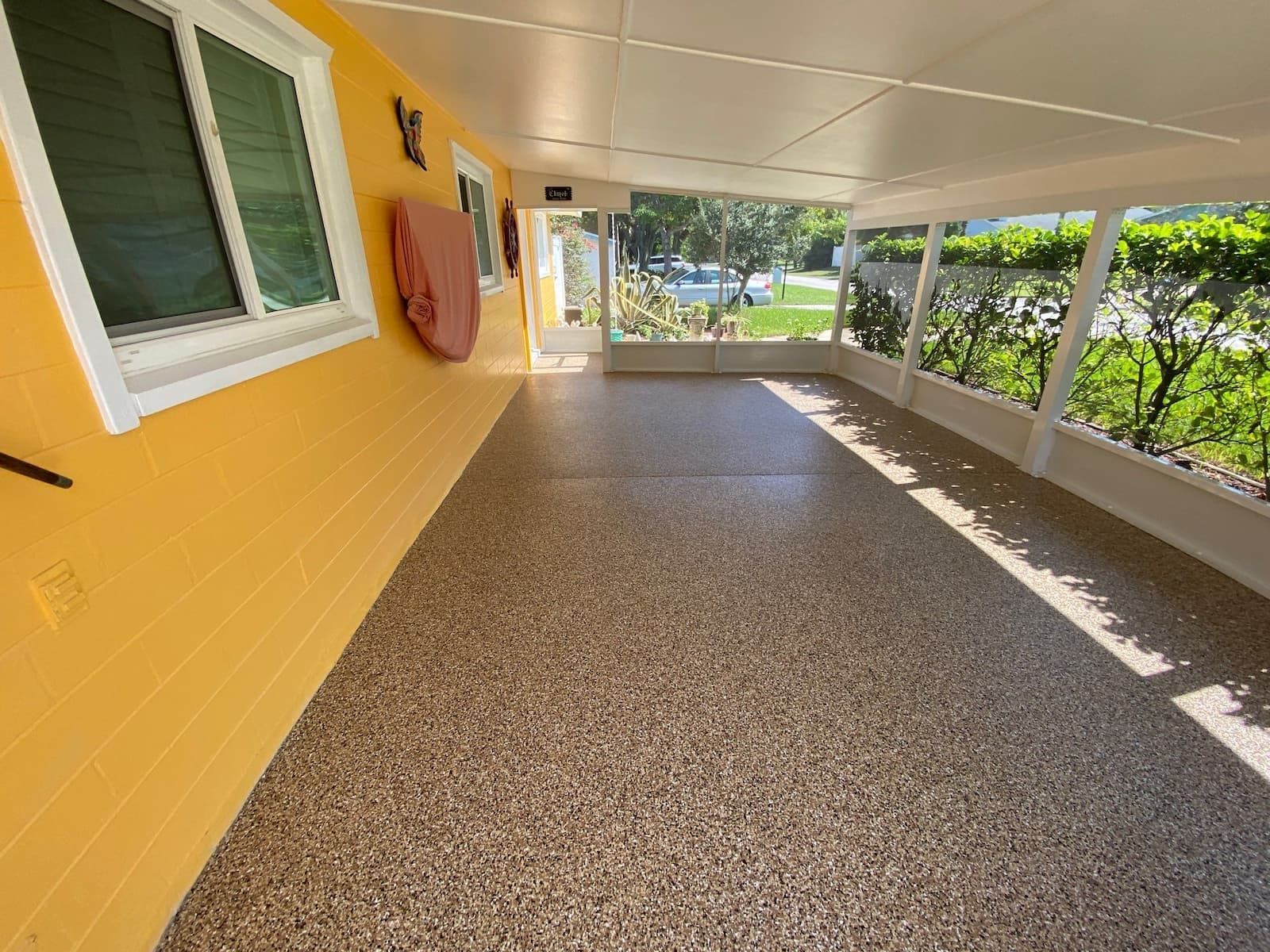
Residential Flooring Applications
Garage floor transformations represent the most popular residential application for polyaspartic coatings. Your garage can become an extension of your living space with a floor that resists car fluids, tire marks, and hot tire pickup.
Basements benefit from polyaspartic's moisture resistance. Unlike some flooring options, these coatings create a barrier that prevents mold and mildew growth in traditionally damp spaces.
Your indoor living areas can also utilize polyaspartic flooring for a modern, sleek appearance. The coating's UV stability means it won't yellow over time, maintaining its appearance for years.
Outdoor patios and pool decks represent another application area. We can create beautiful, durable surfaces that stand up to weather extremes and pool chemicals while remaining comfortable underfoot.
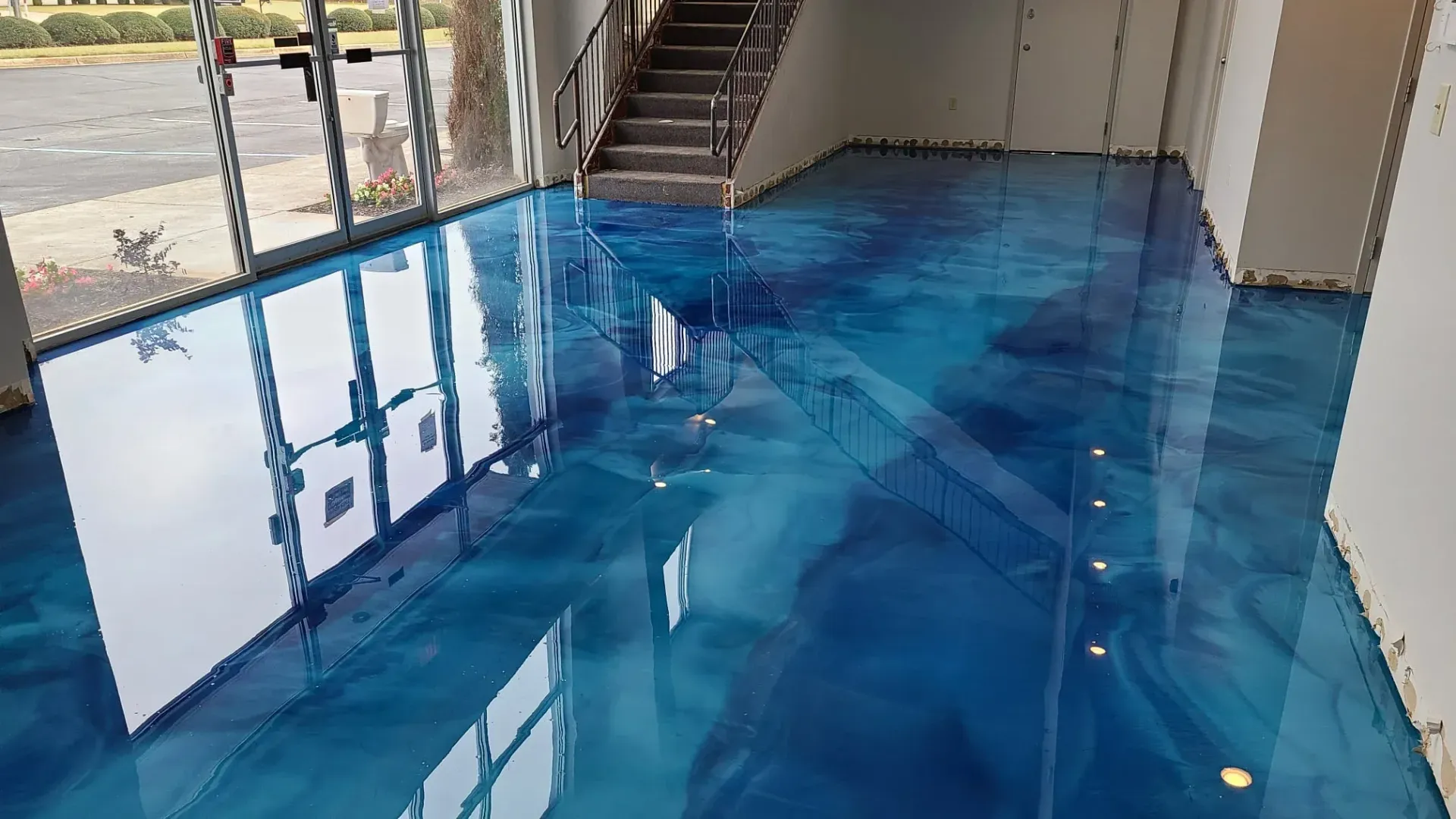
Specialized Applications
Marine environments pose unique challenges that polyaspartic coatings handle exceptionally well. Boat decks, docks, and waterfront properties benefit from the coating's resistance to salt water and UV damage.
Sports facilities choose these floor systems for gymnasiums and weight rooms. The impact resistance and customizable texture options create safe surfaces for athletic activities.
We've installed specialized anti-static polyaspartic flooring in electronics manufacturing and server rooms where controlling static discharge is critical.
Parking structures represent another specialized application. The coating's chemical resistance protects against automotive fluids, road salts, and the constant abrasion of vehicle traffic.
Zoo habitats and aquarium walkways benefit from these coatings too. Your visitors stay safe with non-slip surfaces while the animals enjoy environments that are easy to clean and maintain.
Polyaspartic Floor Coating Process
Proper installation of polyaspartic floor coating requires specific steps to ensure durability and optimal performance. The process involves thorough preparation, precise application techniques, and appropriate curing time.
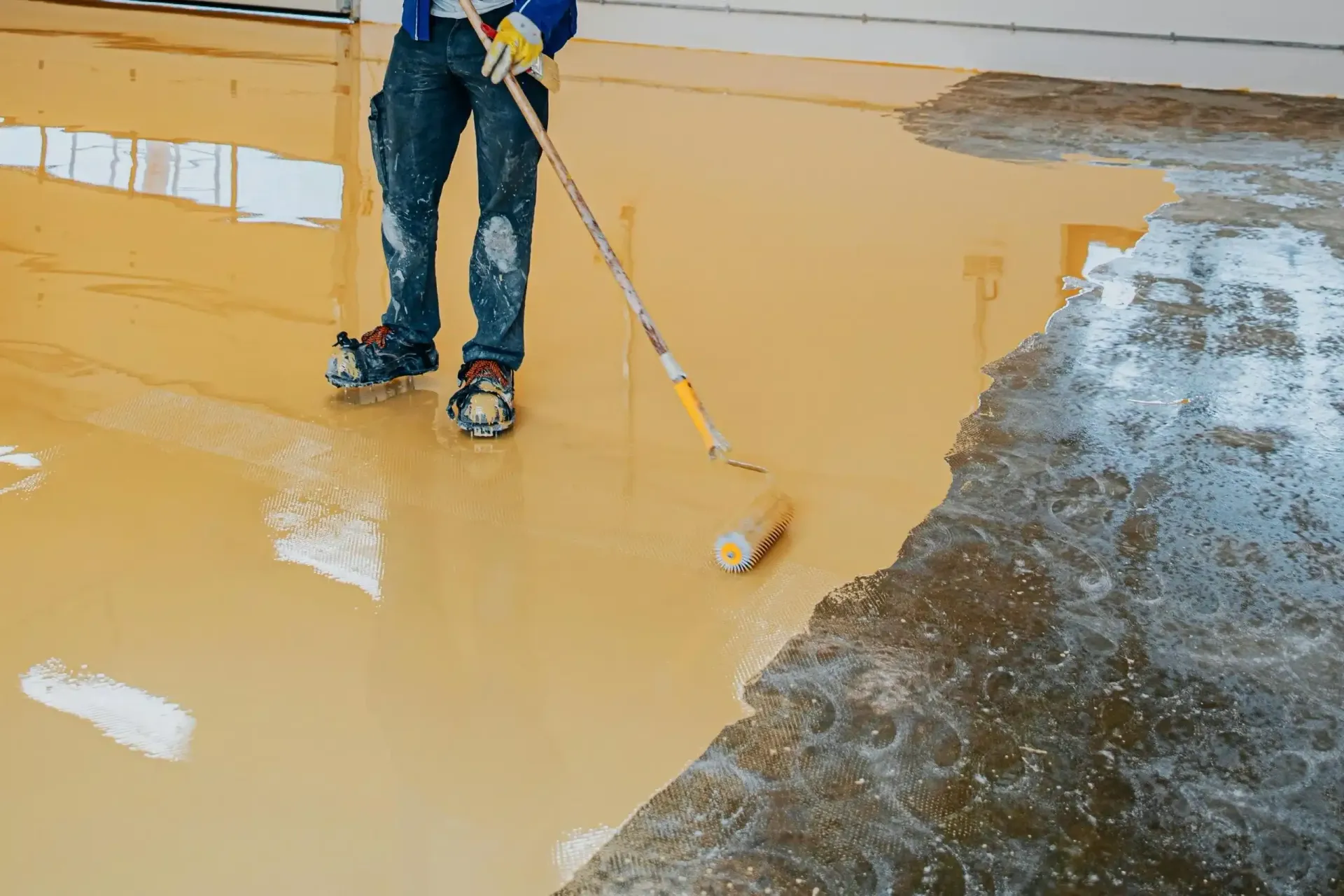
1. Surface Preparation
Before applying polyaspartic coating, we thoroughly clean and prepare the concrete surface. This critical first step ensures proper adhesion and longevity of your floor. We start by removing all dirt, grease, and previous coatings using industrial cleaners and diamond grinding equipment.
Next, we repair any cracks or damages in your concrete. Small cracks are filled with epoxy fillers, while larger issues might require a floor repair overlay. For uneven surfaces, we apply self-leveling compounds to create a smooth base.
The final prep stage involves profiling the concrete through grinding or shot blasting. This creates a textured surface that helps the coating bond properly. We then vacuum and clean the area to remove all dust and debris, leaving a pristine surface ready for coating.
2. Coating Application
We typically apply polyaspartic coatings in multiple layers for best results. The first layer is often a primer that penetrates the concrete and creates a strong foundation. We use special rollers or squeegees designed specifically for polyaspartic application to ensure even coverage.
For decorative floors, we can broadcast color chips or quartz between coats while they're still wet. This adds both visual appeal and texture. For high-traffic areas or garages, we recommend including a non-slip floor option by adding textured materials to the final coat.
Application must be done quickly and efficiently as polyaspartic coatings set faster than other floor coatings. Our professional contractors are trained to work with these fast-setting materials. Temperature and humidity levels must be monitored throughout the process, as they affect setting time and final appearance.
3. Curing and Re-Coat Timing
One major advantage of polyaspartic coatings is their fast-curing properties. Unlike epoxy that may take days to fully cure, polyaspartic floors can often be walked on within 4-6 hours after application. This quick-turnaround installation minimizes downtime for your home or business.
Re-coat timing is crucial when applying multiple layers. We must apply the next coat within the "re-coat window" – typically 1-4 hours after the previous coat. Missing this window could require additional surface preparation before continuing.
Temperature affects curing significantly. In warmer conditions, the coating cures faster, while cooler temperatures slow the process. Our formulations offer low-temperature cure capabilities, allowing installation even in less-than-ideal conditions. The floor typically reaches full chemical and abrasion resistance within 5-7 days, though you can resume light use much sooner.
4. Cleaning and Upkeep
Daily sweeping or dust mopping is essential to remove debris that might scratch your floor's surface. This simple habit prevents abrasive particles from damaging the coating over time.
For regular cleaning, use a pH-neutral cleaner diluted with water. Harsh chemicals can dull the finish and potentially damage your floor sealing system. We recommend mopping weekly for residential floors and daily for commercial spaces.
Spills should be addressed immediately. Though polyaspartic coatings are known for their easy-to-clean surface, prompt attention prevents staining. Simply wipe up spills with a soft cloth or paper towel.
For tougher spots:
- Apply a mild cleaner directly to the stain
- Let it sit for 1-2 minutes
- Gently scrub with a soft brush
- Rinse thoroughly with clean water
Avoid dragging heavy objects across the floor, as this can scratch even abrasion-resistant coating.
5. Repairing and Re-Coating
Despite polyaspartic's durability, damage can occur over time. Small scratches in the clear topcoat option can often be buffed out with specialized polishing compounds that we can recommend.
For deeper scratches or chips, spot repairs are possible. We can match your existing coating and apply it only to the damaged area, blending it with the surrounding floor.
Most polyaspartic floors need re-coating every 7-10 years, depending on traffic and wear. The process involves:
- Thoroughly cleaning the surface
- Light sanding to create adhesion
- Applying a new thin coat
- Allowing proper curing time
Watch for signs that indicate re-coating may be needed:
- Diminished shine
- Visible wear patterns in high-traffic areas
- Increased difficulty in cleaning
- Minor surface scratches throughout
With proper maintenance, your polyaspartic floor's easy maintenance qualities will continue to serve you well for years.
Why Choose Us
At Kansas City Flooring Company, we provide top-quality underlayment services that ensure your vinyl floors look great and last longer. Our professional installation team understands the unique needs of each space. We carefully select the right underlayment materials to address moisture concerns, sound reduction, and comfort underfoot.
You deserve floors that not only look beautiful but also stand the test of time. With our expertise in vinyl flooring underlayment, we help protect your investment while creating a comfortable living environment.
Don't compromise on this essential foundation layer. Our experienced installers follow industry best practices to ensure proper installation every time, preventing issues like uneven floors or premature wear. We serve the entire Kansas City area with reliable, professional flooring services. Contact us today to learn more about our vinyl flooring underlayment options and how we can help with your next flooring project.
Still have a question?
Call us now at (816) 555-0123 or fill out our simple contact form on our website. We'll respond within 24 hours to discuss your specific requirements.