Underlayment Repair in Kansas City, MO
Our underlayment repair service addresses these hidden problems that can affect your home's comfort and value. We make tough floors easy through expert underlayment repairs, using quality materials and techniques to create a stable base for any flooring type.
Many homeowners don't realize that problems like squeaky floors, uneven surfaces, or premature wear often stem from underlayment issues. Our skilled team specializes in gypsum underlayment, waterproofing, and self-leveling underlayments that create the perfect foundation for your new floors. We've helped countless Kansas City residents solve these problems without needing complete floor replacement.
You deserve floors that not only look great but feel solid underfoot for years to come. Our underlayment repair services fix the root causes of flooring problems, not just the symptoms. We provide free consultations to assess your specific needs and recommend the right solution for your home. With our expertise in all flooring types - from hardwood to laminate to tile - we ensure your underlayment repairs integrate perfectly with your existing or new flooring plans.
Repair and Replacement Options
Our specialized underlayment services can match any situation, from quick fixes to complete overhauls.
Temporary Patch Solutions
For small damaged areas, we offer quick repair options using underlayment patch kits. These solutions work well when you're dealing with limited moisture damage or minor tears in your existing underlayment.
Our patch materials are designed to blend seamlessly with your current underlayment. We use specialized fillers for wood subfloors and waterproof patching compounds for areas prone to moisture.
The process takes just a few hours. We clean the damaged area, apply the appropriate patching material, and ensure it's level with the surrounding underlayment. These patches can extend your floor's life by 2-3 years, saving you money and postponing a larger project.
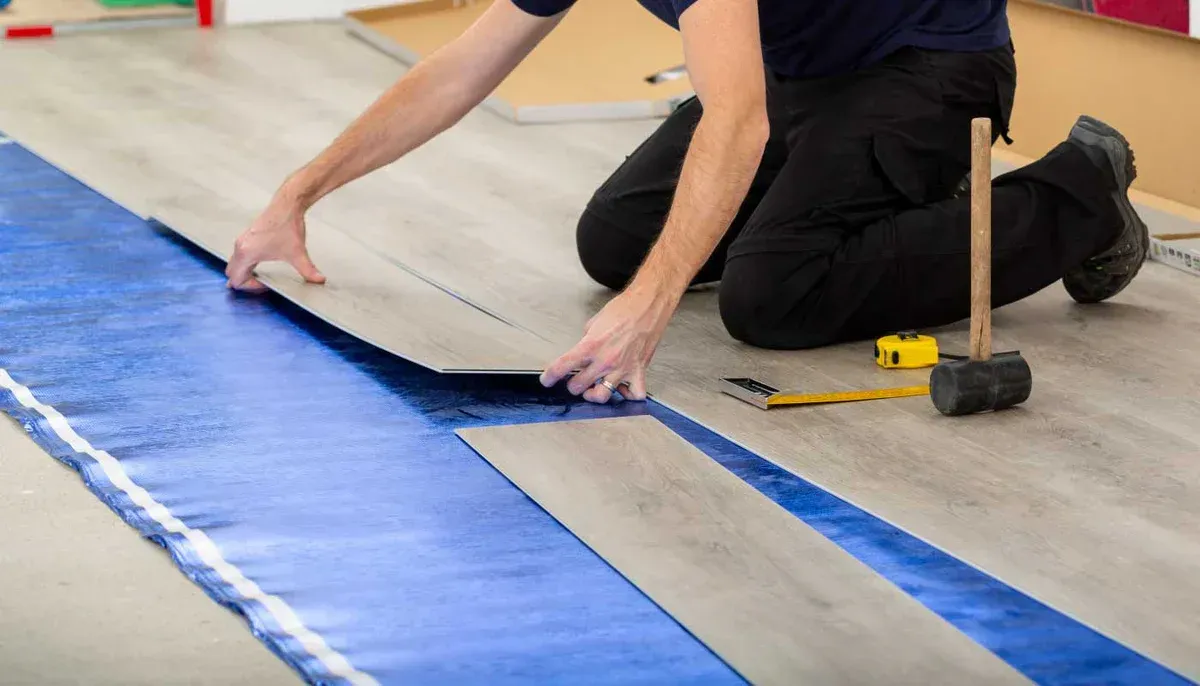
Full Underlayment Replacement
Our team removes all damaged materials down to the subfloor. We inspect for additional problems that might not be visible from above.
We use premium replacement materials matched to your specific flooring type. Cork, foam, plywood, or cement board underlayments are installed with precision to create a perfect foundation.
Full replacement ensures optimal sound insulation and moisture protection while extending your floor's lifespan by 15-20 years.
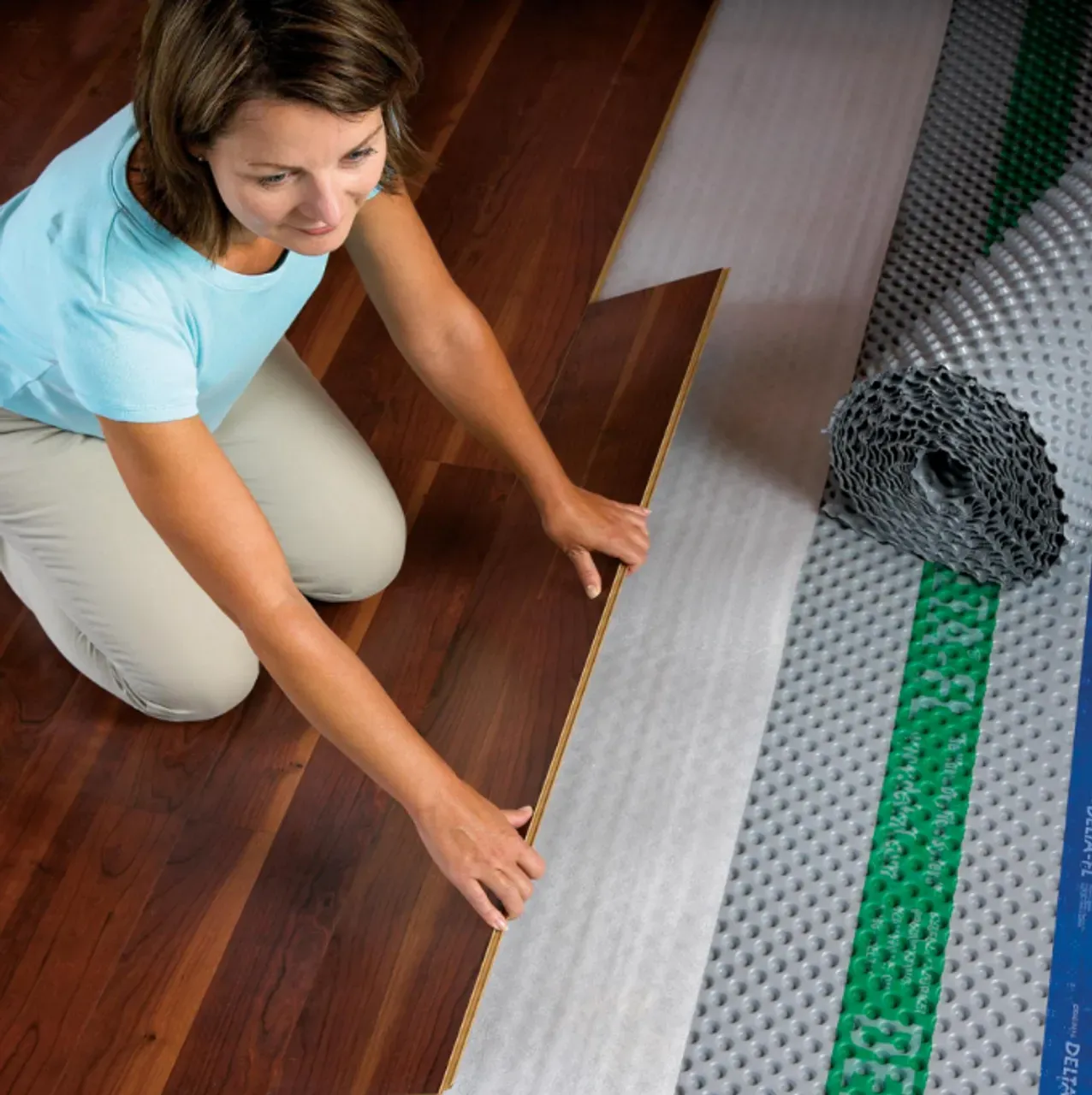
Signs of Underlayment Damage
Identifying underlayment problems early can save you time and money on your flooring project. Damaged underlayment affects your floor's performance, comfort, and longevity.
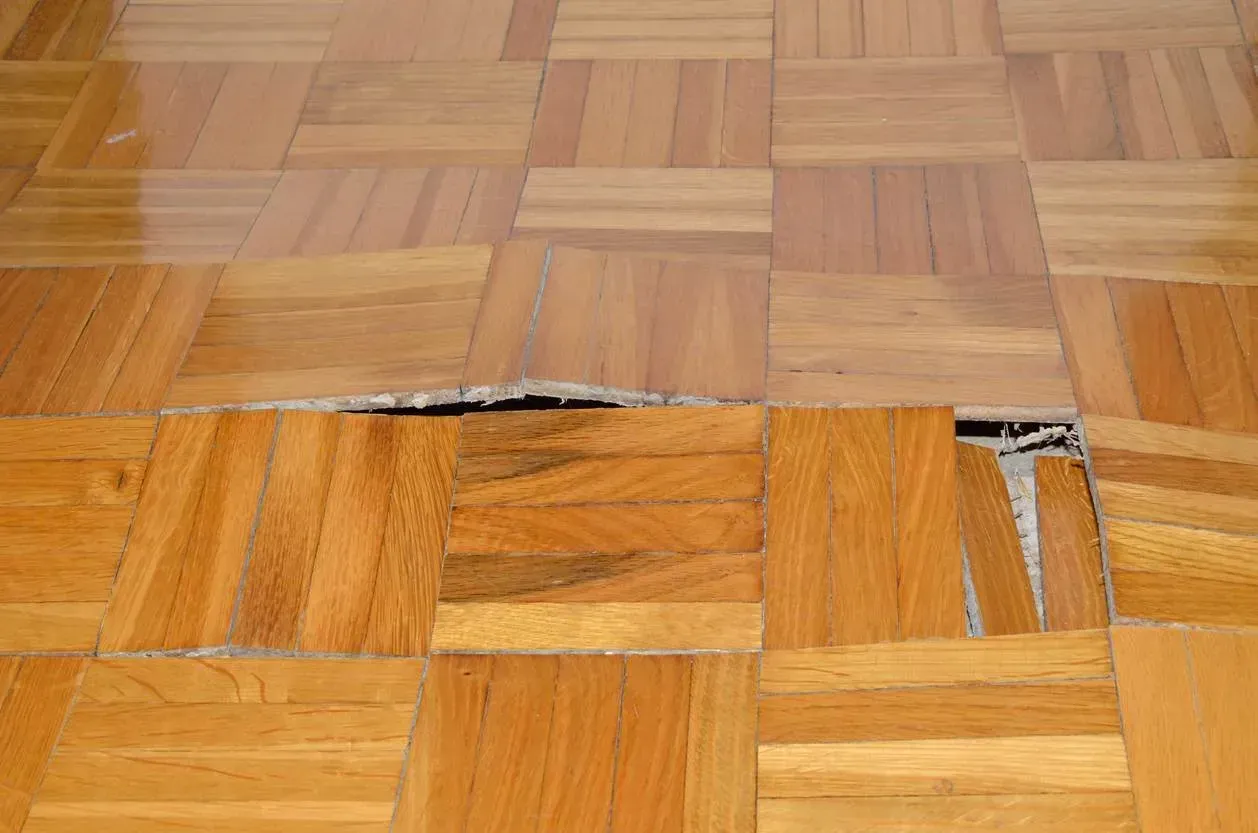
Visible Wear and Tear
Underlayment damage often shows up in noticeable ways in your flooring. You might hear squeaking or creaking sounds when walking across certain areas. These noises typically indicate loose underlayment that's no longer properly supporting your floor.
Uneven spots or dips in your floor surface suggest the underlayment beneath has been compromised. You may notice certain areas feel "soft" or "spongy" underfoot. This happens when the structural integrity weakens.
Visible gaps between floorboards or tiles often point to underlayment issues. We find that homes with high foot traffic show these signs faster, especially in hallways and living rooms. If your floor feels bouncy or unstable, it's time to call us for an inspection.
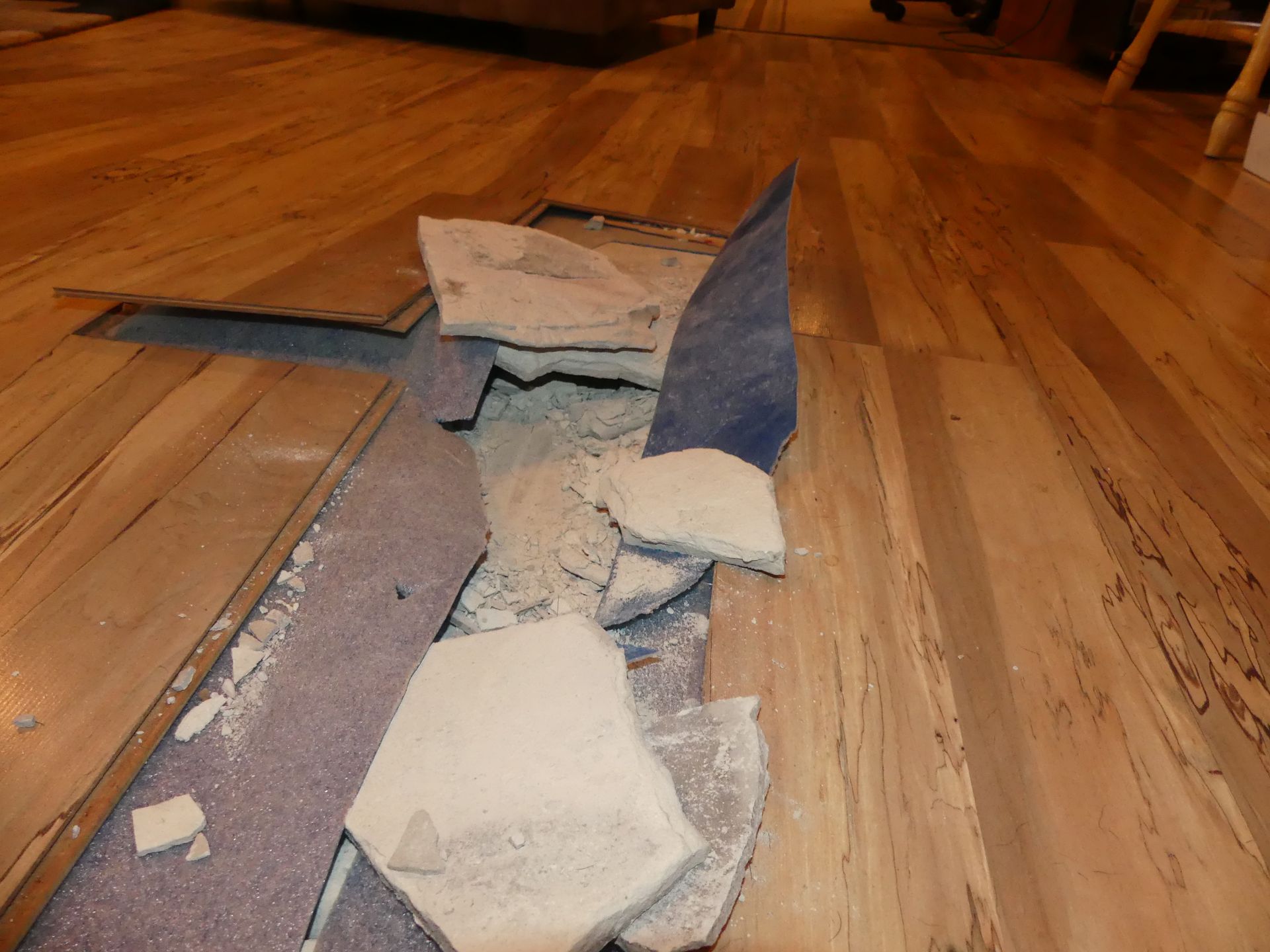
Moisture and Water Damage
Water is the number one enemy of floor underlayment. Discolored areas on your hardwood or laminate flooring often indicate moisture has penetrated to the underlayment below. Look for dark spots, staining, or boards that appear swollen or warped.
Mold or mildew smells coming from your floor signal moisture damage in the underlayment. This is common after flooding or in homes with humidity issues. You might also notice peeling finishes or blistering on your floor's surface.
If your moisture barrier has failed, water can seep into the underlayment and cause severe deterioration. We often find that baseboards showing water damage or mold growth along walls indicate serious underlayment moisture problems that require immediate attention.

Underlayment Deterioration
Plywood and OSB underlayments can rot, creating soft spots that compromise floor stability. You might notice these soft areas when walking across your floor.
Crumbling or flaking underlayment creates uneven surfaces that can damage your finished flooring. Visible signs include buckling floors, separated seams, or tiles that crack without apparent cause.
Chemical breakdown from cleaning products or environmental factors can accelerate deterioration. We recommend checking your underlayment if your floor has been exposed to harsh chemicals or has experienced significant temperature fluctuations.
Termites and other wood-destroying insects can quickly compromise underlayment integrity. If you notice small holes in your flooring or find sawdust-like material, your underlayment might be infested and need immediate repair.
Considerations for Specific Flooring Types
Different flooring materials require specific underlayment approaches to ensure durability and performance. The right underlayment can prevent moisture damage, reduce noise, and extend the life of your floors.
Underlayment for Tile and Hardwood
Tile underlayment needs to provide a stable, flat surface that prevents cracking. We recommend cement backer board for most tile installations, especially in wet areas like bathrooms. This creates a moisture-resistant barrier that protects both the subfloor and tile adhesive.
For hardwood floors, a moisture barrier underlayment is crucial. We use high-quality felt or foam products that help prevent warping and buckling. These underlayments also provide sound dampening benefits, which is important in multi-level homes.
Proper underlayment thickness matters too. Too thin, and your hardwood might develop squeaks. Too thick, and you could have installation issues with door clearances.
Underlayment for Vinyl and Laminate
Vinyl flooring requires smooth, even underlayment since any imperfections will show through. We typically use thin plywood or specialized vinyl underlayment to create the perfect surface. For luxury vinyl, we might recommend cork underlayment for added comfort and sound absorption.
Laminate floors benefit from moisture-resistant underlayment with built-in vapor barriers. This protects your flooring from humidity that rises through concrete subfloors. We offer options with attached padding that improves comfort and reduces noise.
Temperature fluctuations affect these floors significantly. Our premium underlayments include thermal protection to help maintain consistent floor temperatures and prevent expansion gaps.
Proper Use of Adhesives and Sealants
We select high-quality adhesives specifically designed for underlayment applications. Different flooring types require different bonding agents - plywood underlayment needs construction-grade adhesives, while cement board requires thinset mortar.
For seam sealing, we apply waterproof sealants to prevent moisture infiltration. This is especially important in bathrooms and kitchens where water damage is common.
Our team carefully follows manufacturer guidelines for application temperatures and curing times. Many adhesive failures occur when products are applied in improper conditions.
We use notched trowels to ensure even adhesive distribution and proper coverage. Too little adhesive creates weak spots, while too much can cause bumps and uneven surfaces.
Dealing with Subfloor and Joist Issues
We thoroughly inspect subflooring for rot, water damage, and structural weakness before making repairs. Weak spots in subflooring must be addressed before new underlayment installation.
For minor damage, we use floor patch compounds to level depressions and fill gaps. Severe damage requires replacing sections of subflooring entirely.
Joist issues are particularly important to address. We reinforce sagging joists with sister joists or blocking to provide proper support.
When working with concrete subfloors, we check for moisture issues using specialized testing equipment. High moisture levels require vapor barriers or moisture-resistant underlayment.
Eliminating Squeaks and Noise
We identify noise sources by walking the floor and marking problem areas. Most squeaks come from movement between underlayment, subfloor, and joists.
Our primary fix involves special underlayment screws that secure loose layers together without damaging finished floors above. We place these strategically at squeak points.
For persistent squeaks, we access the underside of flooring through basements or crawlspaces. This allows us to apply wood blocks and brackets to stabilize the floor system.
Noise-reduction underlayments with cork or rubber components are excellent solutions for soundproofing between floors. These materials absorb impact noise and vibration.
We also use specialized fasteners with coated shanks that resist loosening over time, preventing future squeaks from developing.
Still have a question?
Call us now at (816) 555-0123 or fill out our simple contact form on our website. We'll respond within 24 hours to discuss your specific requirements.