Subfloor Replacement in Kansas City, MO
These are common signs of subfloor damage that shouldn't be ignored. At Kansas City Flooring Company, we specialize in professional subfloor replacement services that address these structural issues before they become costly problems. Our expert team can identify and replace damaged subfloors, creating a solid foundation for your beautiful new flooring installation.
Subfloor replacement is a critical service that many homeowners don't think about until problems arise. Your subfloor acts as the backbone of your entire flooring system. When it's damaged by water, pests, or age, it can lead to sagging floors, squeaky boards, and even mold growth. We've helped countless Kansas City homeowners restore their floors to perfect condition, ensuring stability and longevity for whatever flooring material you choose.
We understand that finding reliable flooring contractors can be challenging. That's why our team at Kansas City Flooring Company takes pride in our transparent pricing, quality materials, and expert craftsmanship. When you choose us for your subfloor replacement needs, you're getting a local company with deep roots in the Kansas City community. Call us today for a free consultation and discover why we're considered one of the best flooring companies in the Kansas City area.
Steps for Subfloor Replacement
Our team follows a systematic approach that ensures quality results and minimizes disruption to your home.
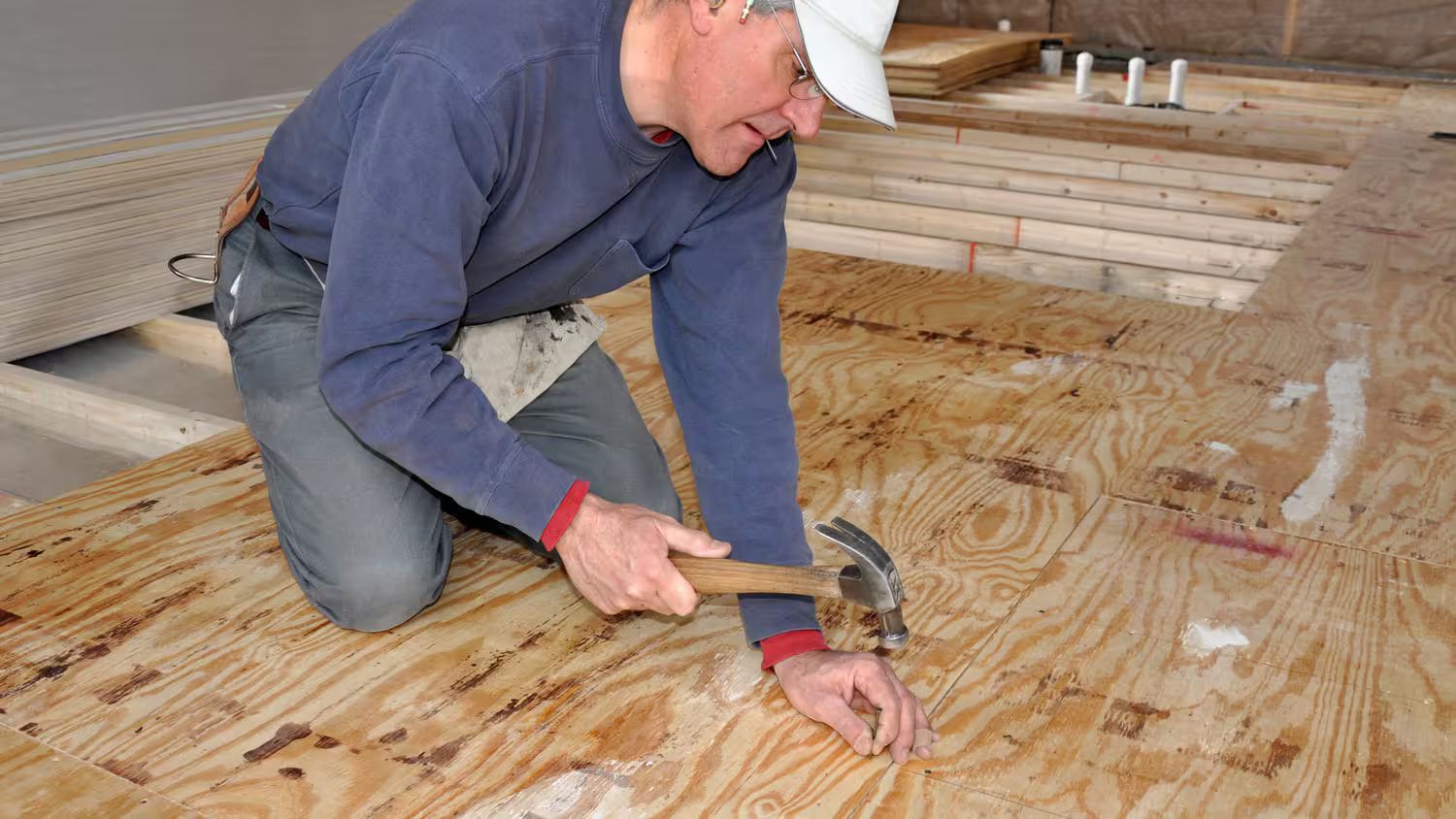
1. Clearing the Work Area
We begin by removing all furniture and belongings from the space where we'll be working. This protects your possessions and gives us room to work efficiently. All flooring materials covering the damaged subfloor must be carefully removed.
For hardwood floors, we use specialized pry bars to lift planks without damaging surrounding areas. Carpet and padding are rolled up and set aside or disposed of according to your preference. We take special care with baseboards and trim, removing them intact when possible for later reinstallation.
Floor patching materials from previous repairs are also removed to ensure we start with a clean slate. Our crew disposes of all debris promptly, keeping your home as tidy as possible throughout the process.
2. Ensuring a Safe Working Environment
Safety is our top priority during every subfloor replacement project. We implement multiple precautions to protect both our workers and your home.
We always shut off electricity to the work area if we'll be using power tools near wiring. Proper ventilation is established using fans to manage dust and fumes from adhesives. Our team wears appropriate safety gear including gloves, eye protection, and knee pads.
Drop cloths and plastic sheeting protect adjacent areas from dust and debris. We create clear pathways through your home for material removal and delivery to prevent accidents or damage to your property.
If your subfloor damage was caused by water or mold, we take extra precautions to test surrounding areas and ensure all affected materials are properly removed and the area is completely dry before installation begins.
3. Disassembling Existing Flooring Layers
We begin by carefully removing your current flooring material. This might be hardwood, laminate, vinyl, or tile. Each material requires specific tools and techniques to prevent damage to surrounding areas.
For hardwood floors, we use specialized pry bars that minimize splintering. Laminate and vinyl typically come up in sections, which we carefully document if any pieces need to be preserved.
Sheet vinyl often hides multiple subfloor issues, so we take extra care during removal. Our team looks for signs of water damage or soft spots that might indicate deeper problems.
After the main flooring is removed, we tackle any remaining adhesives or fasteners. This prep work is crucial for ensuring the new subfloor will have a clean, solid foundation.
4. Addressing Joists and Supporting Structures
Once we expose the subfloor, our inspection becomes more thorough. We check each joist for signs of rot or structural weakness. Rotten joists can't support new materials and must be addressed immediately.
Floor joist upgrades are often necessary in older homes. We might recommend sistering (reinforcing existing joists with new lumber) or complete joist replacement if deterioration is extensive.
We pay special attention to areas around plumbing and HVAC systems. These are common sources of moisture that can damage supporting structures over time.
Our team measures floor levelness at this stage. Uneven joists can cause future flooring failures, so we correct any issues before installing the new subfloor.
5. Choosing the Right Material for the Job
We primarily use two materials for subfloor replacement: plywood and oriented strand board (OSB). Plywood offers excellent strength and moisture resistance, making it ideal for bathrooms and kitchens. It costs a bit more but provides superior durability.
OSB (oriented strand board) is more budget-friendly while still delivering good performance. It works well in most residential applications with normal moisture levels.
The thickness we select depends on your specific needs:
- 5/8" - Standard for most residential applications
- 3/4" - Provides extra stability for tile or stone flooring
- 1" or thicker - For specialized applications or commercial spaces
We always match or upgrade the thickness of your existing subfloor to ensure proper door clearances and transitions between rooms.
6. Laying Down and Securing New Subfloor Panels
Proper installation begins with careful measurements. We cut each panel to fit precisely, leaving 1/8" expansion gaps between panels and at walls.
We use a staggered pattern when laying panels. This prevents weak spots and distributes weight more evenly across your floor structure.
Securing the panels properly is crucial. We use:
- Ring-shank nails or screws specifically designed for subfloors
- A fastener pattern of every 6" along edges and 8" in the field
- Construction adhesive between the joists and panels for extra stability
This combination eliminates squeaks and prevents panels from loosening over time. We take extra care around vents, pipes, and other floor penetrations to ensure a perfect fit.
7. Ensuring Structural Integrity and Compliance
All our subfloor installations meet or exceed local building codes. We understand Kansas City's specific requirements for residential and commercial subfloor installations.
We check floor joist spacing and condition during installation. If joists need reinforcement, we'll address this before laying the new subfloor.
Level and flat surfaces are essential. We use laser levels to ensure the entire subfloor surface is within 1/8" of level across 10 feet. This prevents future flooring problems.
For multi-story buildings, we also consider sound transmission. Adding acoustic underlayment or using specialized subfloor systems can dramatically reduce noise between floors.
Final inspection includes checking all fasteners, testing for squeaks, and verifying the subfloor's stability. You can be confident your new floors will have a solid foundation.
8. Smoothing and Leveling the Subfloor Surface
We begin by sanding any uneven joints or high spots on your new subfloor. This crucial step prevents those annoying squeaks and bouncy spots that can develop over time. Our professional-grade sanders remove all rough edges and splinters that might damage your top flooring.
For concrete subfloors, we use specialized leveling compounds to fill low spots. Wood subfloors sometimes require planing to achieve perfect flatness. We measure with precision tools to ensure the surface variation stays within 1/8 inch over any 6-foot span.
Proper leveling prevents premature wear of your new flooring and extends its lifespan. A smooth subfloor means your laminate won't click when walked on, or your hardwood won't develop gaps between boards.
9. Moisture and Safety Checks
We conduct thorough moisture testing using professional moisture meters on both wood and concrete subfloors. The readings must fall below specific thresholds (typically under 12% for wood) before proceeding.
For areas prone to moisture, we install appropriate vapor barriers and moisture membranes. These protective layers prevent future damage and mold growth under your new flooring.
We carefully tape all seams in the moisture barrier to create a complete seal. This step is especially important in basement installations or areas near bathrooms and kitchens.
Our safety checks also include ensuring all fasteners are properly countersunk and that the subfloor is securely attached to the joists below.
Types of Subfloors and Their Unique Considerations
Plywood subfloors are common in many homes and offer excellent strength and stability. These engineered wood panels typically consist of multiple layers of thin wood veneer. When replacing plywood subfloors, we consider:
- Thickness requirements (typically ¾" for floor joists 16" on center)
- Grade and exposure durability rating
- Proper installation pattern to maximize strength
OSB (Oriented Strand Board) subfloors provide a cost-effective alternative to plywood. These engineered wood panels are made from compressed wood strands arranged in specific orientations. OSB considerations include:
- Slightly lower moisture resistance than plywood
- Typically less expensive than comparable plywood
- Similar structural performance when properly installed
Concrete subfloors present different challenges, often requiring moisture barriers and leveling compounds rather than full replacement.
Additional Services and Considerations
We customize our approach based on your home's specific needs and structural requirements.
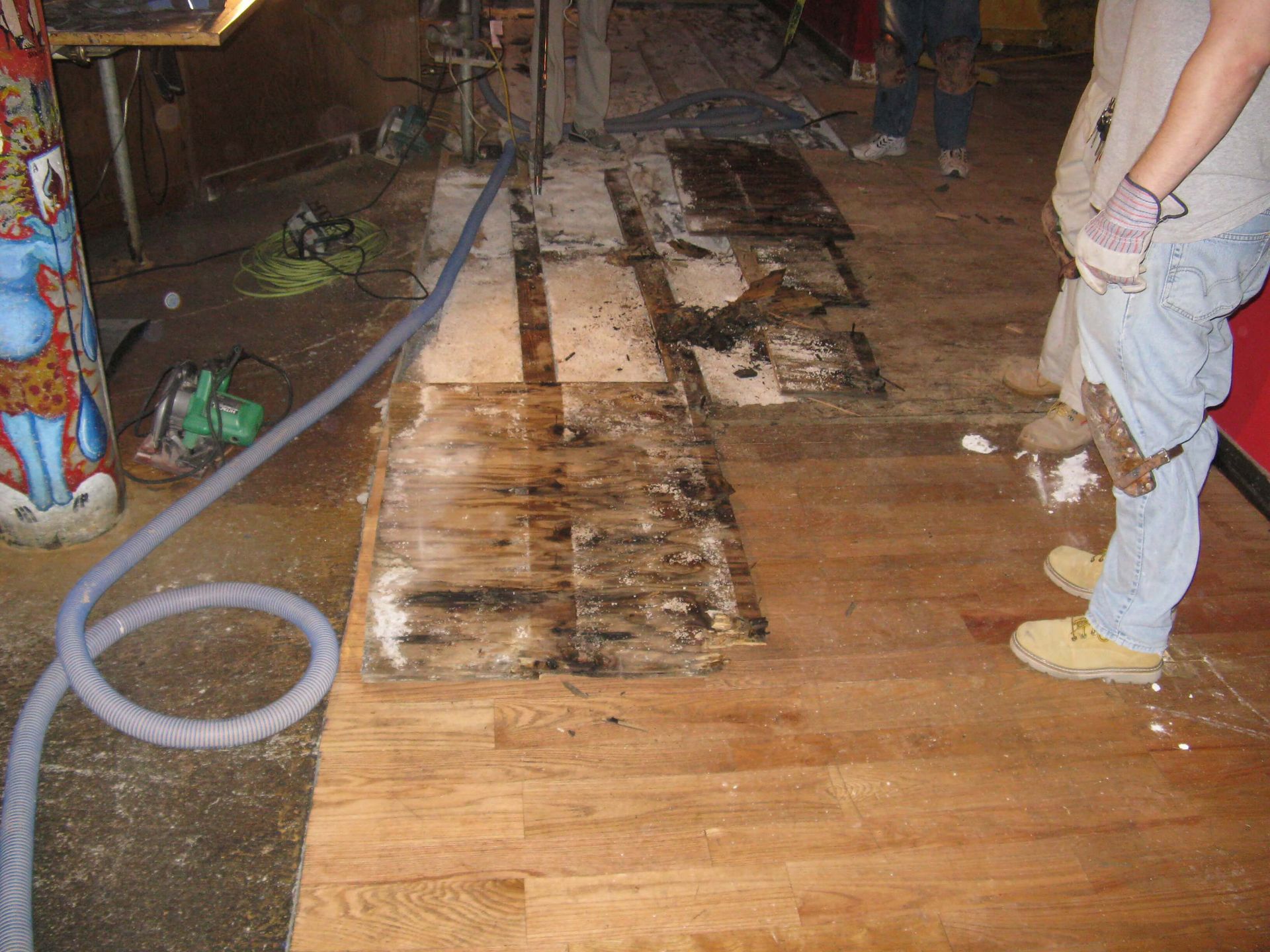
Water Damage and Wood Rot Solutions
Water damage is one of the most common issues we encounter when replacing subfloors. Our team is expertly trained to identify and address all signs of moisture problems and wood rot. We don't just replace the damaged sections—we find and fix the source of the problem.
For homes with significant water exposure, we install water-resistant subfloor materials specifically designed for bathrooms, kitchens, and basements. These specialized materials prevent future damage and extend the life of your flooring investment.
We also provide complete wood rot repair services. This includes removing all compromised materials, treating surrounding wood with anti-fungal solutions, and reinforcing structural elements as needed. Our goal is to create a stable, dry foundation for your new flooring.
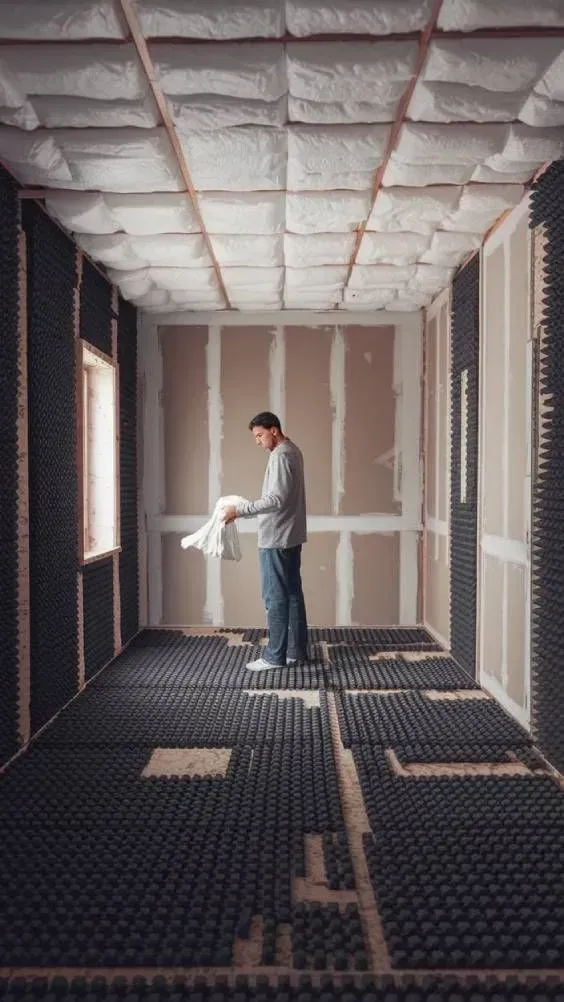
Soundproofing and Insulation Additions
We offer soundproofing upgrades during your subfloor replacement. Our acoustic underlayment options can significantly reduce noise transfer between floors. It is perfect for multi-level homes or apartments.
These sound-dampening materials reduce footfall noise by up to 70% compared to standard subfloors. We use premium cork, rubber, or fiber-based products that absorb vibrations without compromising floor stability.
We also provide under-floor insulation services to improve your home's energy efficiency. This additional layer helps maintain consistent room temperatures and can lower heating and cooling costs. Our team carefully installs insulation materials that won't compress over time, ensuring long-lasting performance.
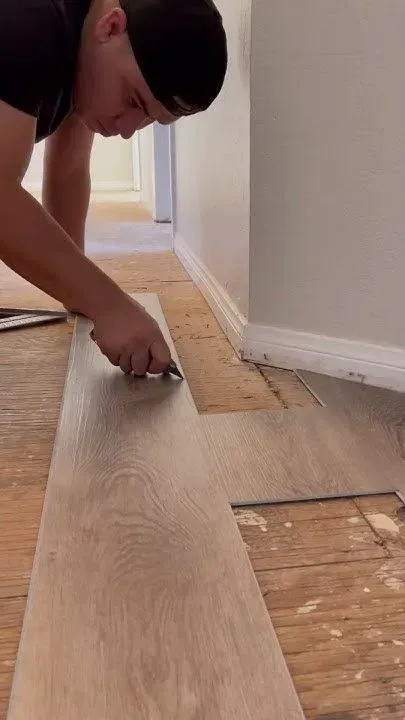
Custom Modifications for Plumbing and Electrical Runs
Your subfloor often needs to accommodate various home systems. We expertly create custom cutouts and channels for:
- Plumbing pipes and drains
- Electrical wiring and outlets
- HVAC ducts and vents
- Radiant heating systems
Our precision cutting ensures proper clearance for all utilities while maintaining structural integrity. We coordinate with your plumber or electrician when necessary to guarantee all modifications meet local building codes.
For homes undergoing renovation, we can reconfigure subflooring to accommodate new layouts or systems. Our team measures and plans all modifications carefully, preventing costly mistakes that could damage your utilities or compromise your flooring.
Why Choose Us
Kansas City Flooring Company stands apart in the soundproof flooring industry with our commitment to excellence and customer satisfaction. We bring together technical expertise, premium materials, and personalized service to ensure your acoustic flooring needs are met with precision.
Satisfaction Guaranteed
Commitment to Quality and Durability
Our installation techniques follow industry best practices to ensure your new subfloor remains level, stable, and moisture-resistant. This attention to detail prevents future issues like squeaking floors, uneven surfaces, or premature deterioration.
We back our subfloor replacement with solid warranties (minimum 2 years), giving you peace of mind in your investment. Many competitors cut corners with low-quality materials that might save money initially but cost more in the long run.
Comprehensive Service from Start to Finish
We handle every aspect of your subfloor replacement project. From initial assessment and material selection to removal of old materials and expert installation of your new subfloor.
Our process begins with a thorough inspection to identify any moisture issues, structural problems, or other concerns that might affect your new floor's performance. We provide detailed, easy-to-understand estimates without pressure tactics.
Experienced Professionals and Customer Satisfaction
Our installation crews average over 10 years of experience in subfloor replacement and flooring services. This expertise allows us to handle even the most challenging projects with confidence and precision.
We maintain a stellar reputation throughout Kansas City, reflected in our consistent 5-star reviews and high customer satisfaction ratings. Our clients appreciate our clear communication and responsiveness throughout the project.
Still have a question?
Call us now at (816) 555-0123 or fill out our simple contact form on our website. We'll respond within 24 hours to discuss your specific requirements.