Vinyl Flooring Underlayment in Kansas City, MO
Installing the right underlayment is crucial for a beautiful, long-lasting floor. At Kansas City Flooring Company, we provide expert vinyl flooring underlayment services that ensure your new floors look amazing and perform well for years to come.
Our professional underlayment installation creates a smooth, level surface that prevents imperfections from showing through your vinyl flooring while adding insulation and noise reduction benefits. Many homeowners don't realize that proper underlayment is the foundation of any great flooring project. Without it, even the highest quality vinyl can develop problems like uneven wear, loose sections, or premature damage.
We've been serving Kansas City homes and businesses with top-quality flooring solutions for years. Our team specializes in all aspects of vinyl flooring installation, including selecting the right underlayment for your specific needs. Whether you're installing luxury vinyl plank (LVP) or sheet vinyl, we understand the unique requirements of each product. We take pride in our careful preparation work that makes the difference between an average installation and a flawless one that stands the test of time.
Short title
The Role of Underlayment in Vinyl Flooring
Underlayment provides several key benefits for your vinyl flooring installation. First, it creates a smooth, level surface that prevents imperfections in your subfloor from showing through your new vinyl. This is especially important with thin vinyl products. Underlayment also adds sound insulation, reducing the noise of footsteps and other impacts. This makes your home quieter and more comfortable.
Additionally, underlayment offers moisture protection for your floors. It creates a barrier that helps prevent moisture from seeping up from the subfloor, which can damage vinyl flooring over time. For floating vinyl floor systems, underlayment provides the necessary support that allows the floor to expand and contract with temperature changes without buckling or separating.
Factors to Consider for Underlayment Selection
When selecting vinyl flooring underlayment, subfloor type matters most. Concrete subfloors need moisture barriers to prevent dampness from reaching your vinyl. Wood subfloors benefit from underlayments that provide stability and prevent squeaking. For bedrooms or living rooms, sound-dampening underlayments reduce noise transfer. Basements require waterproof barriers to protect against moisture seepage.
Thicker underlayments (2-3mm) provide better sound insulation and comfort underfoot. However, too thick can create instability with vinyl plank flooring. While basic foam underlayments start at $0.30 per square foot, premium options with multiple benefits can cost up to $1 per square foot. We help you find the best value for your specific needs.
Vinyl Flooring Underlayment Installation Process
We follow a systematic approach that ensures durability and optimal performance of your new floors.
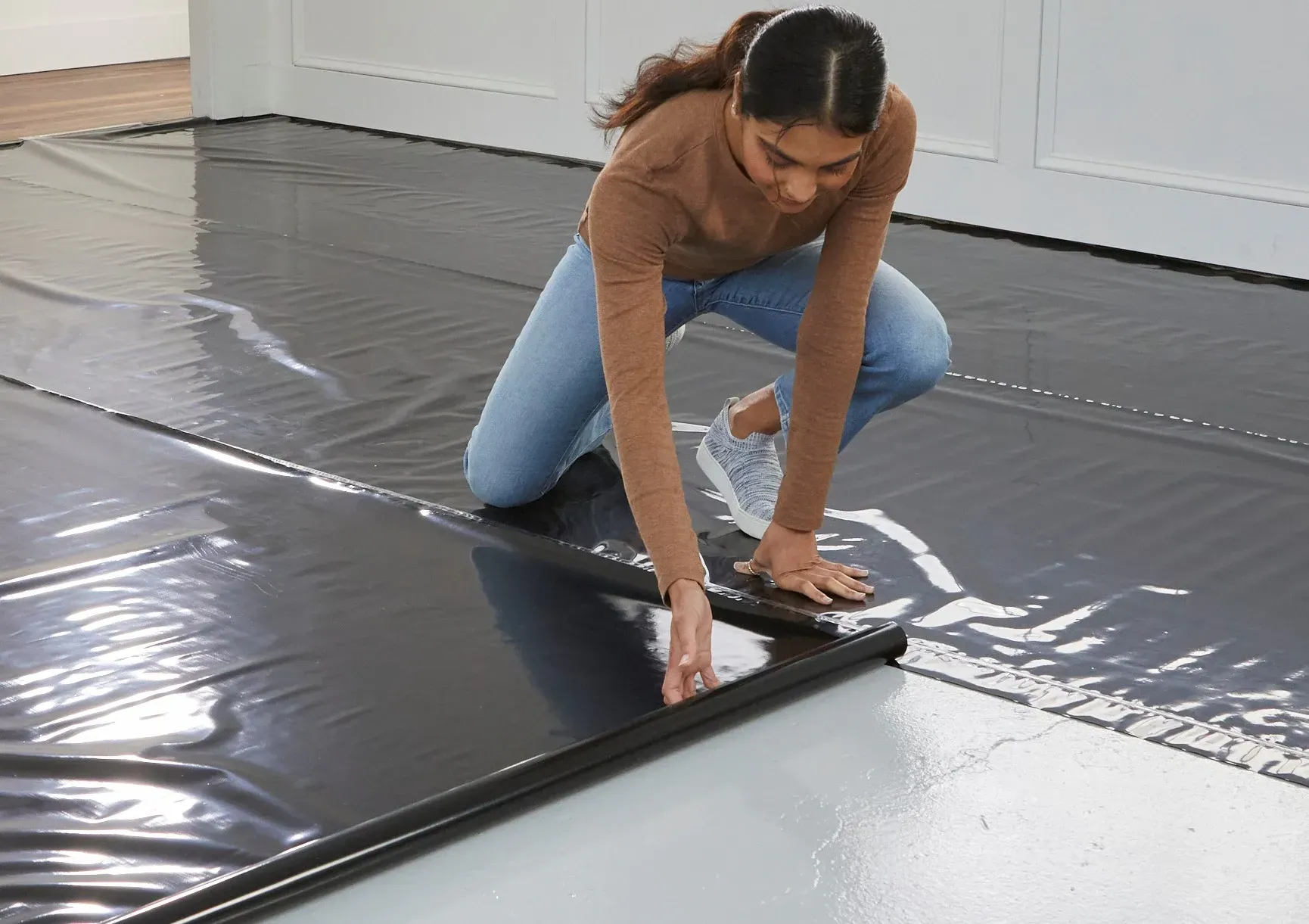
1. Assessing the Condition of the Subfloor
We begin every installation by thoroughly examining your existing subfloor. Our technicians look for signs of damage including cracks, warping, or rotting areas that could affect the new flooring. We check for loose boards, protruding nails, and areas where the subfloor might be uneven.
For concrete subfloors, we inspect for cracks and crumbling sections. Large cracks could indicate structural issues that need addressing before installation continues.
Wood subfloors require checking for stability and proper attachment to floor joists. A bouncy or squeaky floor often signals problems that need fixing.
We also evaluate the cleanliness of your subfloor, as debris can create bumps under your new vinyl flooring.
2. Subfloor Repair Techniques
Once we've identified problems, our team implements appropriate repair techniques. For wood subfloors, we secure loose boards with screws to eliminate squeaks and movement. Damaged sections are replaced with matching materials.
For cracked concrete, we use specialized fillers designed for flooring applications. These products create a smooth, stable surface that won't affect your vinyl flooring over time.
In cases of severe damage, we might recommend partial replacement of the subfloor. This ensures a solid foundation for your new flooring.
We also address any pest damage, particularly with wood subfloors. Termite or water damage requires thorough removal of affected materials.
3. Leveling the Subfloor
A level subfloor is crucial for vinyl flooring installation. We use professional-grade self-leveling compounds for concrete floors with dips or uneven areas. These products flow into low spots, creating a perfectly flat surface.
For wood subfloors, we sand down high spots and use floor leveling compounds in low areas. Our team pays special attention to transitions between rooms to ensure seamless flooring.
We check levelness using professional tools including laser levels and straightedges. Our standard allows for no more than 3/16" variation over 10 feet.
Proper leveling prevents future issues like buckling or premature wear in your vinyl flooring. It also helps avoid damage to click-lock systems in luxury vinyl products.
4. Moisture Testing and Barrier Solutions
Excess moisture is vinyl flooring's worst enemy. We conduct comprehensive moisture testing on all subfloors before installation begins. For concrete, we use calcium chloride tests and electronic moisture meters to check humidity levels.
Wood subfloors are tested with pin-type moisture meters to ensure moisture content is below 12%.
If we detect excess moisture, we implement appropriate barrier solutions. This may include vapor barriers, moisture-resistant underlayments, or specialized sealants.
For persistent moisture issues, we might recommend addressing the source through improved ventilation or drainage solutions. This protects not only your new flooring but your home's structural integrity.
Our moisture barriers are selected based on your specific situation and the manufacturer's recommendations for your chosen vinyl flooring.
5. Steps for DIY Installation
First, ensure your subfloor is clean, dry, and level. Remove all debris and vacuum thoroughly. Test for moisture levels using a moisture meter—readings should be below 4% for wood subfloors.
For peel and stick underlayment, remove the backing and press firmly to the subfloor, working from one end of the room toward the exit. Avoid overlapping sheets.
When installing foam underlayment, lay it perpendicular to the direction your vinyl planks will go. Leave a small gap (about ¼ inch) at walls to allow for expansion.
For cork underlayment, acclimate the material in your home for 48-72 hours before installation. Use a utility knife to cut pieces to fit, and secure with recommended adhesive or tape at the seams.
Stagger the seams of your underlayment to prevent them from lining up with your vinyl plank seams.
6. Professional Installation
When you choose Kansas City Flooring Company for underlayment installation, we start with a thorough assessment of your subfloor conditions. We test moisture levels and determine if a vapor barrier is needed based on readings.
Our professionals will arrive with all necessary tools and materials. We'll move furniture, remove existing flooring, and properly prepare the subfloor—filling cracks, sanding rough spots, and ensuring it's completely level.
We select the appropriate underlayment type for your specific flooring choice and room conditions. For high-moisture areas, we install specialized underlayments with enhanced vapor barriers.
The installation process typically takes 1-2 days depending on your space size. We work efficiently while maintaining precision. Our team minimizes disruption to your home and cleans up completely when finished.
We provide clear instructions on caring for your new floors after installation is complete.
The Importance of Underlayment in Floor Performance
Underlayment serves as the hidden foundation that dramatically improves how your vinyl flooring performs long-term.
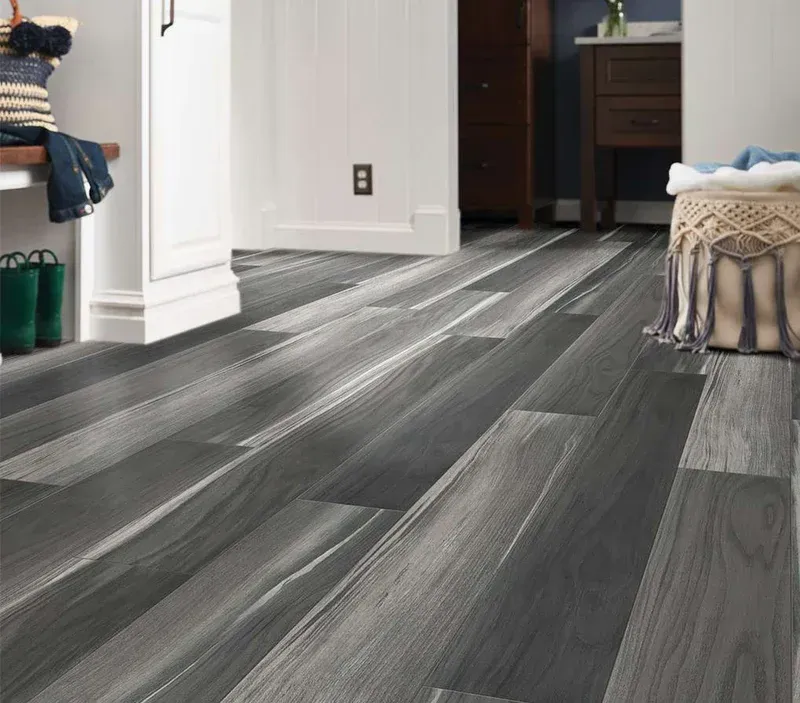
Enhancing Acoustic Performance
Proper underlayment significantly reduces noise transmission between floors. We install specialized acoustic underlayment products that can reduce impact sound by up to 20-25 decibels, making your home noticeably quieter.
Sound Insulation Ratings (STC and IIC) measure how effectively underlayment blocks different types of noise. Our premium underlayments typically achieve IIC ratings above 55, exceeding most building code requirements.
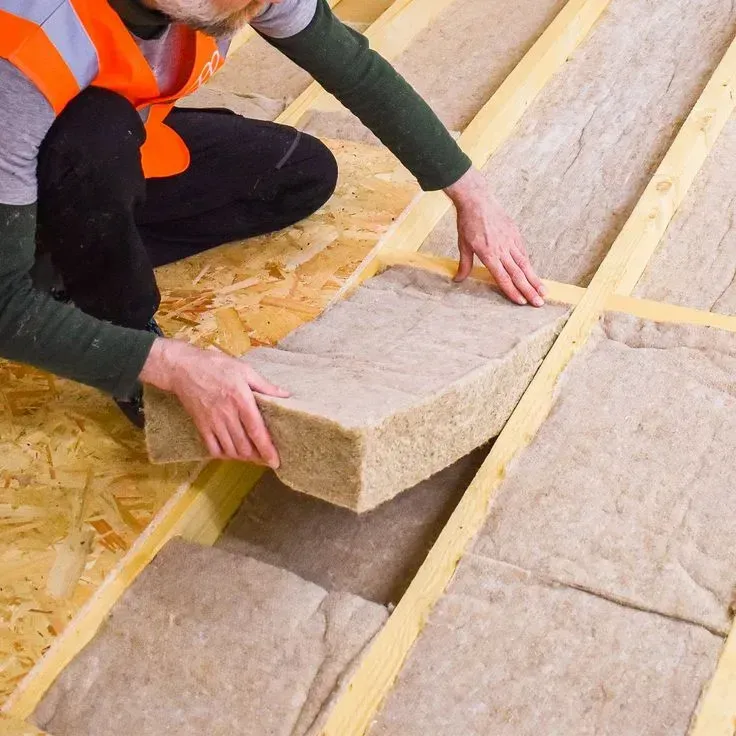
Moisture Protection and Dampness Prevention
Moisture is vinyl flooring's worst enemy. Underlayment creates a crucial barrier against moisture damage in several ways:
Water vapor constantly rises from concrete subfloors, even in seemingly dry conditions. Our vapor barriers block this moisture from reaching your vinyl planks, preventing warping, buckling and mold growth.
We install underlayment with built-in antimicrobial properties in bathrooms, kitchens, and basements. These areas need extra protection from spills and humidity that can damage floors over time.
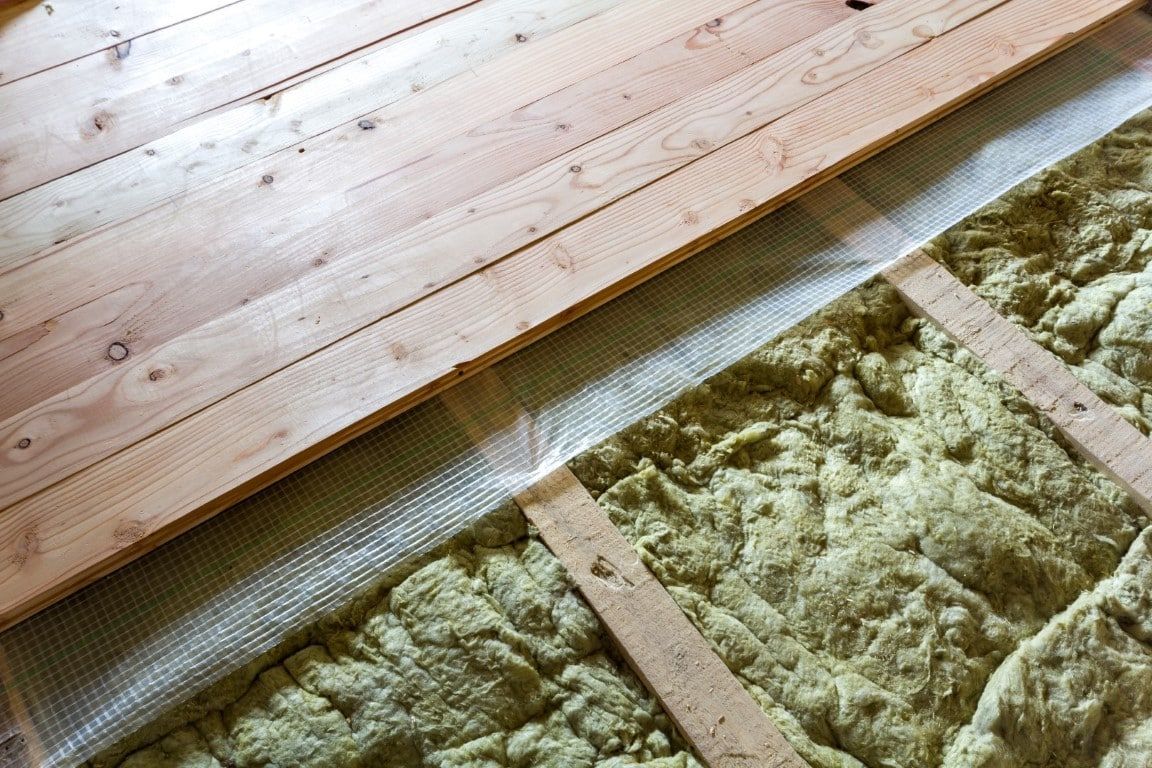
Thermal Insulation and Comfort
Your floor's comfort depends largely on its underlayment. The thermal properties create a warmer, more comfortable surface underfoot.
Thermal underlayment reduces cold transfer from concrete subfloors by up to 15 degrees. This makes a noticeable difference during Kansas City winters when floor temperature significantly impacts home comfort.
The cushioning effect also makes standing and walking more comfortable. We offer underlayment options with varying densities to match your specific comfort needs.
Why Choose Us
At Kansas City Flooring Company, we provide top-quality underlayment services that ensure your vinyl floors look great and last longer. Our professional installation team understands the unique needs of each space. We carefully select the right underlayment materials to address moisture concerns, sound reduction, and comfort underfoot.
You deserve floors that not only look beautiful but also stand the test of time. With our expertise in vinyl flooring underlayment, we help protect your investment while creating a comfortable living environment.
Don't compromise on this essential foundation layer. Our experienced installers follow industry best practices to ensure proper installation every time, preventing issues like uneven floors or premature wear. We serve the entire Kansas City area with reliable, professional flooring services. Contact us today to learn more about our vinyl flooring underlayment options and how we can help with your next flooring project.
Still have a question?
Call us now at (816) 555-0123 or fill out our simple contact form on our website. We'll respond within 24 hours to discuss your specific requirements.